AS Industries : votre fournisseur de pièces en moulage par injection métal
Le moulage par injection métal (MIM)
Le moulage par injection métal (MIM ou Metal Injection Molding) est un procédé technologique d’injection de poudres métalliques ou céramiques et de liant polymère. Le procédé MIM permet de gagner en précision et en productivité de fabrication des pièces usinées en métal.
Ce procédé de fabrication s’inspire de l’injection plastique, réputée pour son degré de liquéfaction de la matière permettant de fabriquer des pièces au travers de moules complexes nécessitant un haut degré de précision.
L’injection de métal via le procédé MIM permet de se rapprocher du degré de précision permise par l’injection plastique, afin de produire des séries en métal réalisées dans des moules complexes.
Quelques exemples de poudres métalliques utilisées pour l’injection de métal en poudre fondu :
L’injection métallique permet de travailler avec ces matériaux :
- Acier inoxydable (AISI 316L) – Numéro atomique : 26 – Utilisé dans les applications médicales, dentaires et aérospatiales. Il offre une résistance élevée à la corrosion et aux températures élevées.
- Titane (Ti6Al4V) – Numéro atomique : 22 – Utilisé dans les applications aérospatiales et médicales en raison de sa légèreté et de sa résistance à la corrosion.
- Aluminium (AlSi12) – Numéro atomique : 13 – Utilisé dans les applications automobiles, électriques et électroniques en raison de sa légèreté et de sa conductivité thermique et électrique élevées.
- Cuivre (CuCrZr) – Numéro atomique : 29 – Utilisé dans les applications aérospatiales et nucléaires en raison de sa conductivité thermique et électrique élevées et de sa résistance à la corrosion.
Il existe également de nombreux autres alliages de métaux qui peuvent être utilisés en injection métallique, tels que le nickel, le tungstène, le cobalt, etc.
Les conditions optimales d’utilisation dépendent des propriétés spécifiques de chaque alliage et peuvent varier en fonction de facteurs tels que la température, la pression et la composition de la poudre.
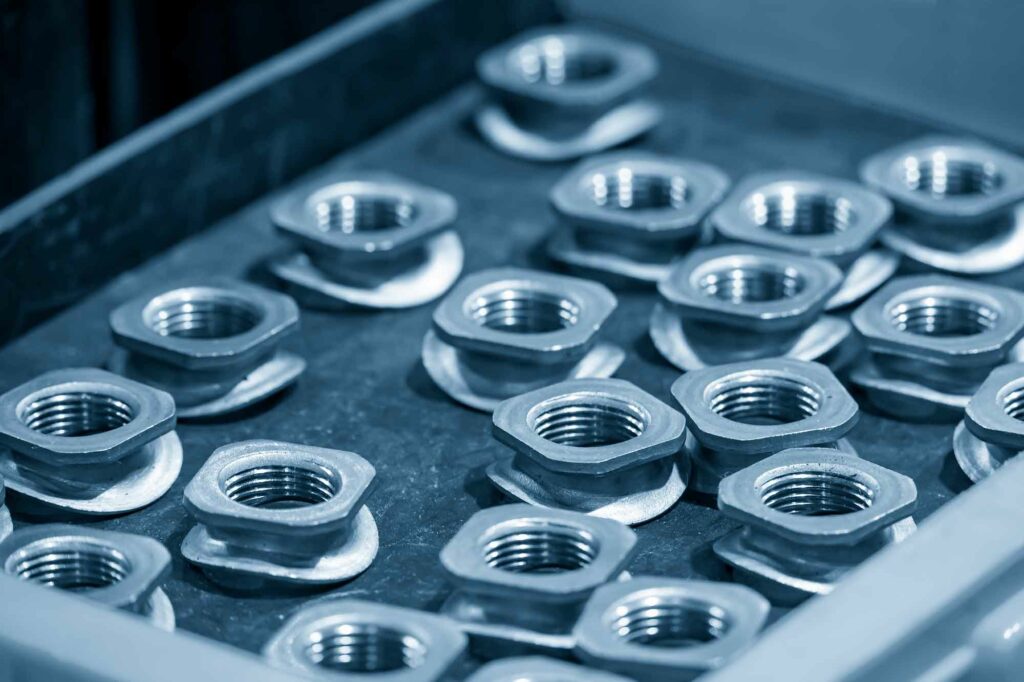
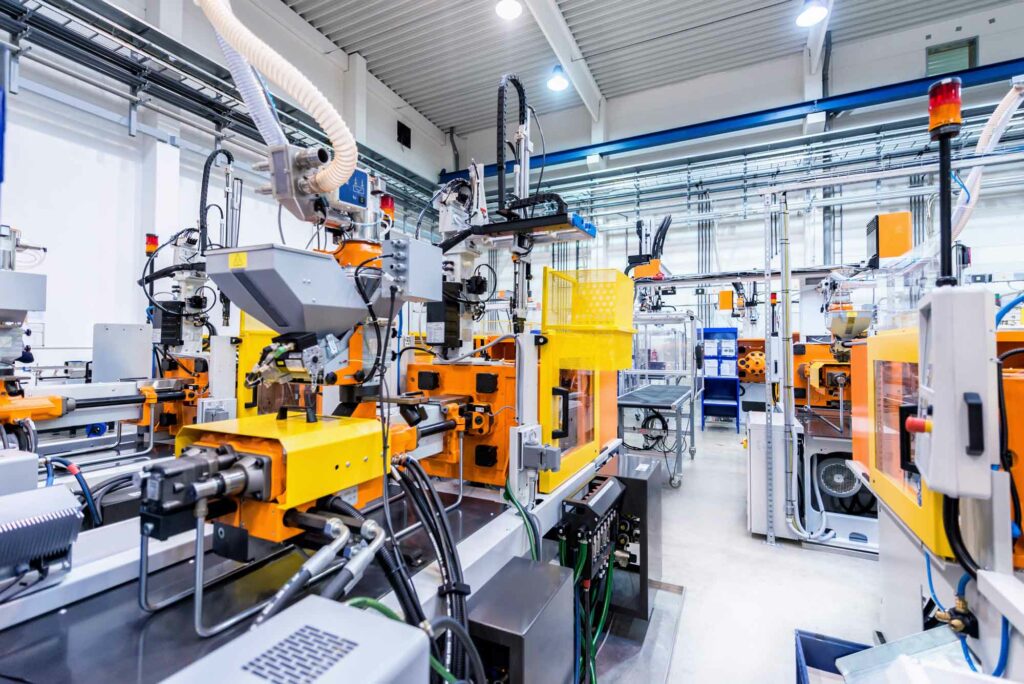
Les alliages nécessitent l’utilisation de divers liants
Pour les poudres métalliques dans le cadre de la réalisation de fonderie, les liants communs utilisés sont les suivants :
- Liants à base de cire : C’est le liant le plus couramment utilisé. Il est facile à manipuler et peut être utilisé pour une variété de formes de pièces. Les avantages incluent une faible viscosité, une excellente mouillabilité et une faible teneur en cendres. Les inconvénients comprennent des pertes de cire lors de la combustion, une faible résistance mécanique et une faible résistance thermique.
- Liants à base de polyéthylène glycol : Ce liant est également communément utilisé pour les poudres métalliques. Les avantages incluent une haute résistance mécanique, une excellente mouillabilité et une faible teneur en cendres. Les inconvénients comprennent une faible résistance thermique et une forte dépendance à la température.
- Liants à base de polymères : Ces liants sont souvent utilisés pour les pièces nécessitant une haute précision dimensionnelle. Les avantages incluent une haute résistance mécanique et une grande stabilité dimensionnelle. Les inconvénients comprennent une faible mouillabilité et une faible résistance à la chaleur.
Exemples de compatibilité avec les poudres métalliques :
- Pour l’acier inoxydable (AISI 316L), les liants à base de cire et à base de polyéthylène glycol sont généralement utilisés.
- Pour l’aluminium (AlSi12), les liants à base de cire sont souvent utilisés en raison de leur excellente mouillabilité.
- Pour le cuivre (CuCrZr), les liants à base de polymères sont souvent utilisés pour leur haute précision dimensionnelle.
Nos pièces mécaniques réalisées en injection de poudre métalliques (MIM) sont certifiées ISO9001 et EN9100
Le fabricant pour les pièces mécaniques de haute précision
AS Industries vous propose la fabrication de vos pièces en MIM (Metal Injection Molding). Ce procédé adapté pour les petites pièces de précision, vous permettra de réaliser des pièces et de bénéficier de propriétés exceptionnelles sur la résistance et l’usure des métaux.
Le moulage par injection de poudre métallique vous offrira un large panel de possibilité de conception pour façonner des pièces complexes adaptées à la moyenne et grande série tout en réduisant les reprises d’usinage.
Cette technologie adaptée pour la petite, moyenne et grande série vous permettra de réduire les reprises d’usinage, les frais de finition ainsi que le recours à des techniques de montage/assemblage coûteuses.
Notre procédé de MIM convient pour divers domaines d’application tels que l’horlogerie / bijouterie, lunetterie ou encore le médical avec des instruments chirurgicaux et d’autres secteurs comme la téléphonie et l’informatique etc.
Les aspects techniques du MIM :
- Petites pièces légères pesant de 0,3g à 150g
- Des composants réalisés avec une épaisseur de paroi allant de 0,2 mm.
- État de surface : Ra < 1,5 µm
- Possibilité de réaliser de petits et grands alésages, alésages transversaux
- Possibilité de filetages intérieurs et extérieurs, de contre-dépouilles et dentures
- 25% à 65% de d’économie par rapport aux procédés standards
- Nette réduction des frais de fabrication des composants complexes
- Résistance mécanique identique à celle des pièces fabriquées de manière
conventionnelle
Notre panel de matières :
Les métaux utilisés sont généralement des aciers faiblement alliés, aciers inoxydables et aciers à outil.
Nos métaux :
- Fers
- Alliages de fer
- Inox
*Autres matières sur demande.
Nos réalisations
Notre laboratoire pour répondre à vos exigences :
Nous sommes également garants de la conformité de vos livrables grâce à nos contrôles qualité effectués dans notre laboratoire de contrôle. Sur demande, nous sommes en mesure de vous fournir un certificat de contrôle et un certificat matière.
Les étapes d’une injection métal réussie
Opérations secondaires :
- Le traitement thermique
Un traitement thermique est un procédé industriel qui vise à modifier la structure physique et/ou chimique d’un matériau en l’exposant à des températures élevées ou basses pendant une période de temps déterminée. Les traitements thermiques peuvent avoir plusieurs objectifs tels que l’amélioration des propriétés mécaniques, la résistance à la corrosion, ou encore la modification de la microstructure du matériau pour le rendre plus dur ou plus résistant. Les traitements thermiques sont couramment utilisés dans l’industrie pour la production de pièces métalliques, la fabrication de verre, ou encore la cuisson des aliments.
- Le traitement de surface
Le traitement de surface est fait sur une pièce mécanique pour satisfaire des propriétés d’emploi voulues et lui conférer une fonctionnalité spécifique.
- L’aspect de surface
- Décoration
- La résistance à la corrosion
- La résistance au frottement La résistance à l’abrasion/érosion
- La résistance à la fatigue
- L’aptitude au collage
Les avantages de l’injection métal
L’injection métal procure :
- Rapidité de fabrication et de livraison (donc rentabilité pour l’entreprise productrice et le client final).
- Précision dans la conception ( fonctionnement inspiré de l’injection plastique permet une grande flexibilité, l’expliquer simplement).
- Répétabilité des pièces : dimensionnel assuré
- Les moules sont solides et répliquent de grandes séries sans se déformer.
Le choix des matériaux pour la fabrication du moule doit être adapté aux matériaux coulés pour assurer une bonne adhérence et une résistance à l’abrasion.
- De manière générale, les tolérances géométriques appliquées à la fonderie dépendent à la fois de l’alliage utilisé et du type de procédé de fonderie utilisé. En termes de fonderie sous pression, les tolérances géométriques les plus couramment appliquées pour l’acier inoxydable (AISI 316L) sont de l’ordre de ±0,2 mm pour les dimensions extérieures et de ±0,4 mm pour les dimensions intérieures. Pour l’aluminium (AlSi12), les tolérances géométriques peuvent être encore plus serrées, de l’ordre de ±0,1 mm pour les dimensions extérieures et de ±0,2 mm pour les dimensions intérieures. Pour le cuivre (CuCrZr), les tolérances géométriques sont généralement assez similaires à celles appliquées à l’acier inoxydable.
- En ce qui concerne la fonderie en coquille, les tolérances géométriques peuvent être encore plus serrées que celles appliquées à la fonderie sous pression. Pour l’acier inoxydable (AISI 316L), par exemple, les tolérances géométriques peuvent être de l’ordre de ±0,1 mm pour les dimensions extérieures et de ±0,2 mm pour les dimensions intérieures. Les tolérances pour l’aluminium (AlSi12) sont similaires à celles appliquées à la fonderie sous pression, tandis que celles pour le cuivre (CuCrZr) peuvent être légèrement plus larges, de l’ordre de ±0,2 mm pour les dimensions extérieures et de ±0,3 mm pour les dimensions intérieures.
- Enfin, pour la fonderie par cire perdue, les tolérances géométriques peuvent également être assez serrées, mais peuvent varier considérablement en fonction de la complexité de la pièce. Pour l’acier inoxydable (AISI 316L) et l’aluminium (AlSi12), les tolérances géométriques peuvent être de l’ordre de ±0,1 à ±0,2 mm pour les dimensions extérieures et de ±0,2 à ±0,4 mm pour les dimensions intérieures. Pour le cuivre (CuCrZr), les tolérances géométriques peuvent être similaires à celles appliquées à la fonderie en coquille.